See how Autodesk customers are using Autodesk® Simulation CFD software.
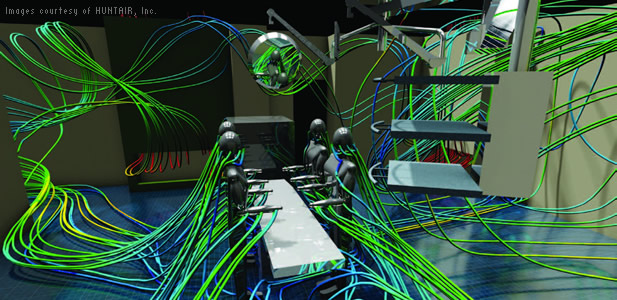 |
HUNTAIR, Inc.: Cleaner Operating Rooms
Oregon-based HVAC firm uses Autodesk simulation software to help the healthcare industry reduce post-operative infections by designing operating rooms like cleanrooms.
"Autodesk Simulation CFD Advanced helps us show healthcare facilities what is actually going on with airflow in their ORs versus what should be happening theoretically. This is really important when challenging an industry to rethink its practices."
—Kevin Schreiber, Global Director of Healthcare, HUNTAIR, Inc.
Project Summary
Imagine a fully loaded Boeing 747 crashing 4 times a week, every week, with no survivors. Over a 52-week period, that would result in about 100,000 lives lost. That’s roughly the same number of deaths in the United States each year that can be attributed to infections contracted in hospital operating rooms (ORs). According to recent estimates by the Centers for Disease Control and Prevention, these infections, also known as nosocomial or healthcare-associated infections (HAIs), can cause or contribute to 99,000 U.S. deaths annually. In addition to the devastating impact on patients’ families, the fatalities and treatment of over 290,000 surgical site infections per year cost the U.S. healthcare system billions of dollars—and yet, they are preventable.
HUNTAIR, Inc. is on a mission to raise awareness about the problem of HAIs. A subsidiary of the CES Group, Inc., the largest group of custom heating, ventilation, and air conditioning manufacturers in North America, HUNTAIR designs and manufactures specialized HVAC systems used in critical industrial environments. Its CLEANSUITE® system, inspired by cleanrooms used in the semiconductor and pharmaceutical industries, is challenging the healthcare industry to rethink how air is delivered to a sterile surgical setting. Armed with computational fluid dynamics (CFD) models created in Autodesk® Simulation CFD Advanced software, HUNTAIR is showing hospitals how airflow over patients in the OR can be optimized to achieve better contamination control—and potentially save thousands of lives and lower treatment costs annually by reducing post-operative complications due to HAIs.
|
|
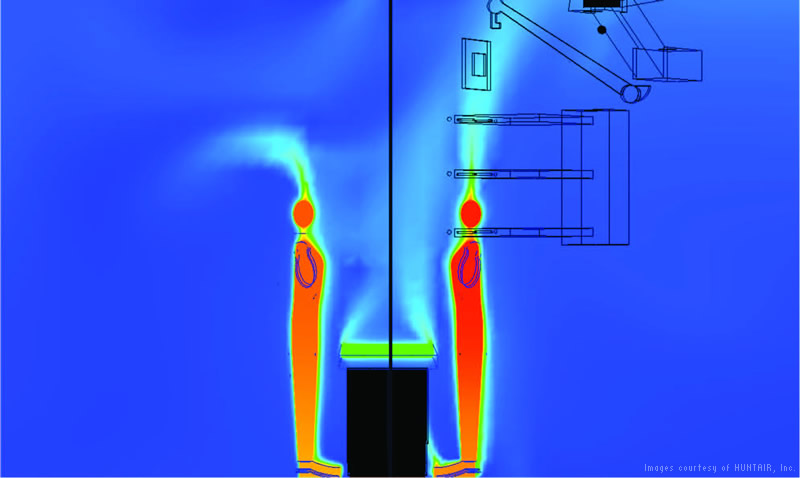 |
The Challenge
HUNTAIR has a history of innovation in designing and manufacturing custom air handling and cleanroom systems, and its products already have helped to improve airflow in healthcare facilities. It was the first to invent an “integrated” fan array solution—FANWALL TECHNOLOGY®—that replaces large fans with a more efficient and cost‑effective array of smaller fans. Many healthcare facilities have adopted this technology because it is quiet, energy-efficient, low-maintenance, and provides redundancy—benefits that are especially important in the OR environment.
The idea for the CLEANSUITE system evolved a few years ago, when HUNTAIR was involved with an OR project for a hospital in Colorado. “I was working with an engineer who was very familiar with our cleanroom offering and our approach to contamination control,” says Kevin Schreiber, global director of healthcare for Tualatin, Oregon-based HUNTAIR. “We got to thinking, ‘Why not apply the same technology used in semiconductor and pharmaceutical cleanroom environments to the operating room?' It would be the perfect application.”
When HUNTAIR engineers began designing the CLEANSUITE system, their research quickly revealed that standard airflow guidelines for ORs, like those from the American Society for Healthcare Engineering (ASHE) and the American Society of Heating, Refrigerating, and Air Conditioning Engineers (ASHRAE), do not address airborne contaminant levels. “The ASHE and ASHRAE standards are primarily concerned with how much air is being pumped into the space, and where it’s coming from and going to,” Schreiber explains. “However, they don’t talk about air cleanliness standards at all.”
In a typical OR environment, air can flow across the biggest contaminate in the room—the surgical staff—and then over the patient. That air can contain millions of squamous cells (skin cells) emitted by every person in the OR—who are also likely carrying contaminates that they picked up from other people in common areas on their way to the surgery suite.
“Your skin is rejuvenating all day, every day. The old stuff dies, falls off, and gets put into the air—about 5 million particles per person, every minute,” says Schreiber. “These particles are less than 0.3 microns in diameter, so they’re in the bacterial range. Think about it: If a typical surgery requires about 5 people in the OR, that means there can be 25 million particles swirling around the patient each and every minute. This is why it’s important to make sure we’re minimizing turbulence and controlling the direction of the air in the OR.”
|
|
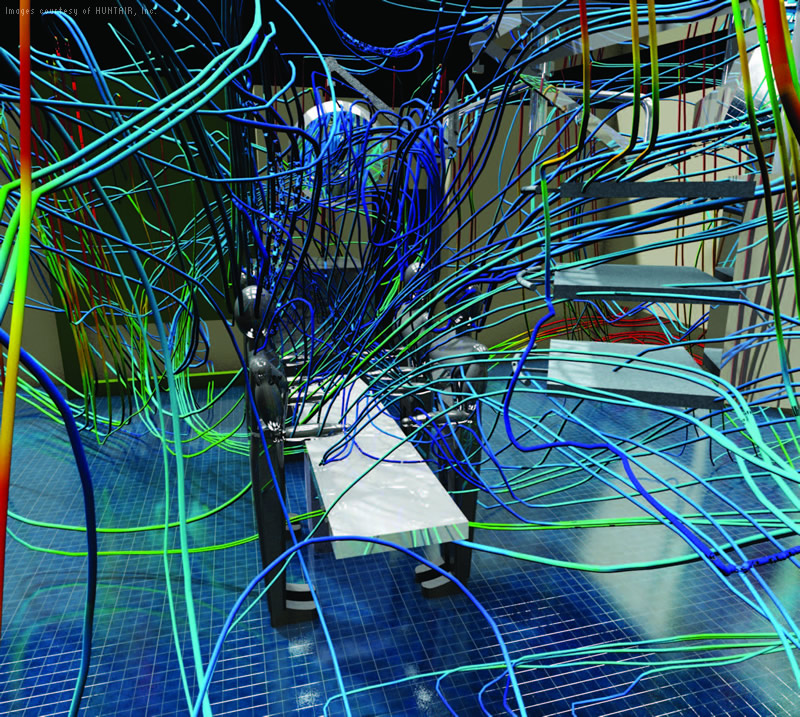 |
The Solution
Laminar flow diffusers are used in ORs to deliver temperature-controlled, HEPA-filtered air over the operating table via a low-turbulence airflow stream. But according to Schreiber, in a standard laminar flow environment with a minimum array design that includes multiple laminar flow diffusers, the air entering into the OR is far from smooth. “A laminar diffuser set in the wrong context does not a laminar system make,” he says. “There are gaps—and there’s a lot of recirculation going on.”
To eliminate the gaps, HUNTAIR’s CLEANSUITE system uses a single-diffuser design, allowing for improved contamination control over the sterile surgical setting. “With CFD simulations performed in Autodesk Simulation CFD Advanced software, you can really see the difference between how the two systems perform,” Schreiber says.
The CLEANSUITE system can deliver the same FPM (feet per minute) that is required, and can also maintain the air’s temperature from when it enters the OR all the way down to the table and the patient. The air then flows away from the patient. “In a standard laminar flow environment, the air being delivered can vary as much as 10°F due to the thermal effects of lights and people,” says Schreiber. “With the CLEANSUITE system, the temperature can be maintained. If the air is 62°F when it enters the room, that’s the temperature it is when it reaches the patient.”
Heat transfer is where things can get “a little bit complicated” when designing CLEANSUITE systems, according to Schreiber, because the OR can include so many heat-emitting elements—such as people. “We usually have to do some pretty detailed studies,” he says. “The 3D models we create have to include the table, the people in the space, the equipment, the booms, the lights, and then the heat signatures from all of those things, as well.”
|
|
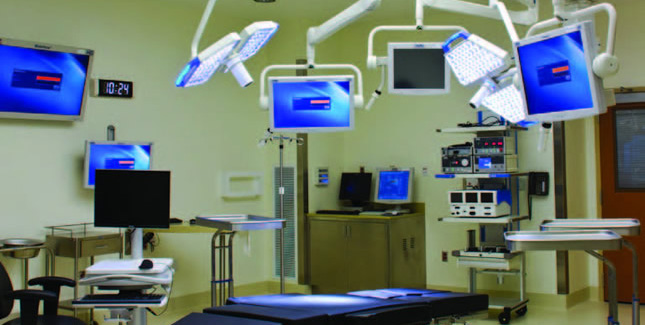 |
Up in the Air
A major consideration in the design of the CLEANSUITE system was placement of equipment for delivering laminar airflow. “You can’t have equipment standing on the floor in the OR because it creates a hazard and takes up valuable space,” says Schreiber. “That’s why hospitals mount things to the ceilings in ORs—equipment booms, monitors, light booms, and so on.”
For its semiconductor product, HUNTAIR had created a structural element to support automated material handling systems (AHMS)—and this got Schreiber thinking. “One of our semiconductor clients uses big robots that shoot through the facility, carrying wafers from place to place, and those all hang directly from our ceiling systems. So, I thought, why not add the mounting of these booms and other equipment in the ORs right onto our product?”
HUNTAIR engineers used Autodesk® Inventor® 3D mechanical design software to model the CLEANSUITE system’s modular, ceiling-hung plenum with integrated filtration, electrical, piping, and structural equipment supports. Schreiber says, “With this approach, we not only have airflow and air delivery, but also a UL-listed light fixture, and a structural interface between that equipment and the building structure. Nobody else is doing anything like it for the OR environment.”
HUNTAIR custom designs each CLEANSUITE system, which installs in a fraction of the time it takes to implement a traditional field-built system, according to Schreiber. “This translates to cost savings for healthcare facilities, and can help them move more quickly from a construction project to a fully functional, revenue-generating facility,” he says.
|
|
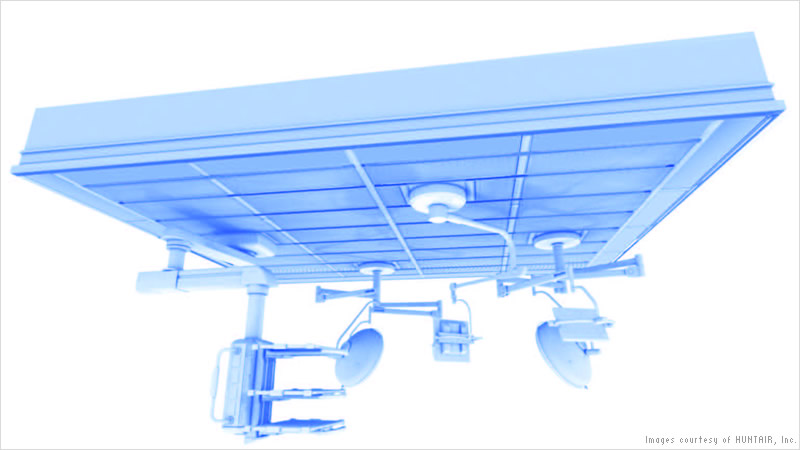 |
Inspiring Change
HUNTAIR introduced the CLEANSUITE system in the fall of 2011. The healthcare industry is not known for being quick to embrace change—especially if it means letting go of long-standing practices—but the CLEANSUITE is already gaining support. For example, integrated managed care consortium Kaiser Permanente is now recommending that the CLEANSUITE system be used throughout its network for both new and retrofit construction projects of ORs.
Compelling CFD models that HUNTAIR created within Autodesk Simulation CFD Advanced software played a key role in influencing Kaiser Permanente’s decision, according to Schreiber. “We developed an executive summary to explain how the CLEANSUITE system is different, and why we think it works better,” he says. “Showing airflow models created with Autodesk Simulation CFD Advanced helped Kaiser Permanente’s corporate leadership understand how the semiconductor and pharmaceutical industries look at contamination control and how these practices can improve air quality in the OR and reduce HAIs.”
Schreiber adds, “Autodesk Simulation CFD Advanced helps us show healthcare facilities what is actually going on with airflow in their ORs versus what should be happening theoretically. This is really important when challenging an industry to rethink its practices.”
|
|
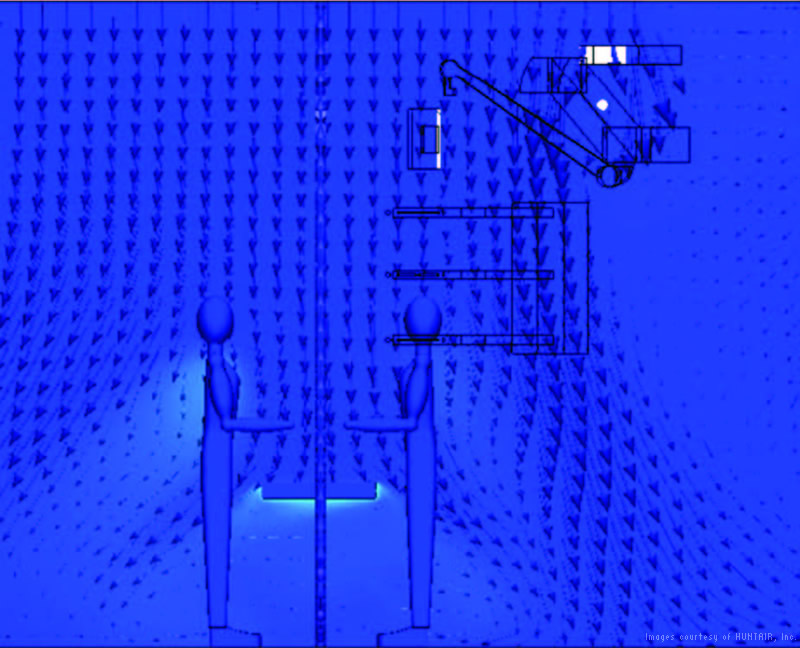 |
The Result
HUNTAIR has already built and installed more than 15 CLEANSUITE systems for healthcare providers. It is now working on designs for several other healthcare facilities, including outpatient surgery centers. “We’re really just starting implementations,” says Schreiber. “But in terms of having an impact on getting people to see how and why they should change the design of the airflow system for their OR environment, we’re really making headway.”
HUNTAIR has been asked by lawmakers in Washington, D.C., to help raise awareness of the need for air cleanliness standards for ORs and plans to present airflow simulations created using Autodesk Simulation CFD Advanced when making its case. “If we want to save lives and reduce healthcare costs, we need to learn from semiconductor and pharmaceutical companies and establish national standards for addressing airborne contaminant levels,” says Schreiber. “That’s what we’re after—and Autodesk software is helping us prove that a solution like the CLEANSUITE system does make a difference.”
Schreiber adds that using Autodesk software strengthens their case in another way—credibility. “That’s probably the most important thing,” he says. “We’re trying to bring this important issue to the forefront, of course, but we’re also selling a product. We have to be very careful that the data we’re providing is not biased in any way. Having Autodesk technology as a part of the process lends credibility to what we’re saying, and that’s huge.”
|
|
| |
| |