剪切热引起流动不平衡现象
一、引言
随着塑料制品注塑成型的高效化和精密化成型发展,一模多穴的应用十分普遍,为保证各腔制品的重量、性能等质量指标均匀一致,必须使浇注系统流动平衡,然而在实际中发现尽管模腔的流道在几何上完全对称,但是每腔的流动并不平衡充填,如图一、图二所示。
多模腔模具与几何平衡流道系统设计的流动不平衡问题,其原因长久以来归咎与模具温度的差异。通过一系列的试验与moldflow有限元模流分析,已经证明流动不平衡问题是由于射出充填时,熔融塑料在流道内所产生的不对称剪切分布现象所致。因此将产生各模穴之间包括压力、熔融塑料温度与成型品机械性质的差异。此塑料剪切所造成的流动不平衡效应会因制造条件、材料、流道设计及流道尺寸的不同而差异显著。
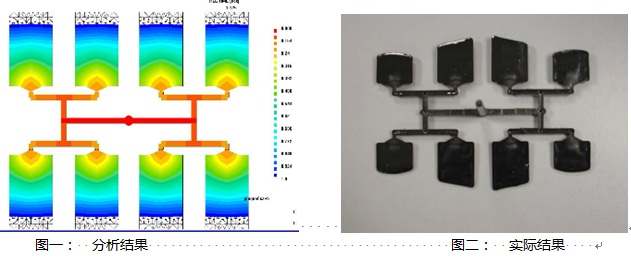
二、流动不平衡产生的缺陷及原因
1、流动平衡:使熔体从注射点到每一个模腔都具有相同的流动距离,如图三所示:
● 流动不平衡将造成相同产品密度、尺寸、重量的差异,从而导致同个产品机械性能的差异及无法装配的现象。
● 非均匀填充容易造成毛刺、缺胶,缩痕、过保压等缺陷,严重影响产品的质量,图四所示:
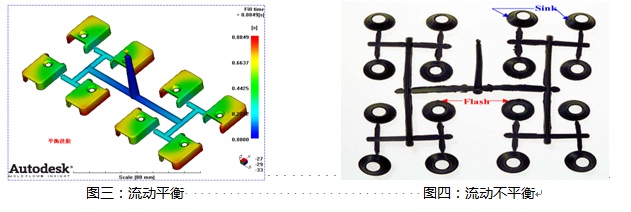
2、影响流动不平衡的因素
模具结构、注塑工艺及塑胶材料都会造成一模多腔的不平衡现象及影响不平衡的程度,如图五所示:
● 模具结构:每腔的排气设计、水路设计的差异将导致填充不平衡的现象。
● 注塑工艺:不同的注塑速度将造成剪切热,剪切热影响各腔的流动。
● 材料:不同材料影响着流动不平衡程度的差异
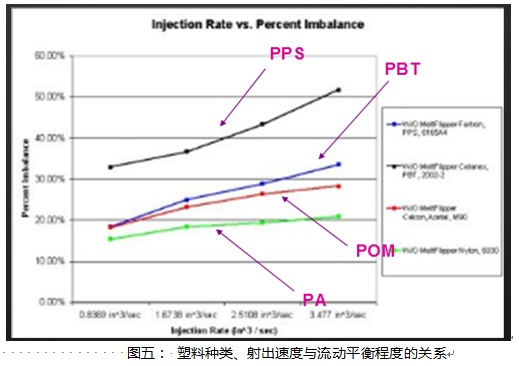
三、剪切热的产生及作用
1、剪切热的产生
● 喷泉流动:熔体在型腔中流动将产生两种流动方式,一种向前推进,一种往外流动,图六所示:
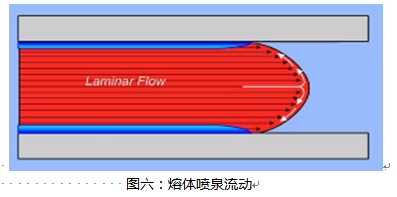
● 剪切速率:沿凝固层内侧剪切速率最大,将产生剪切热,如图七所示:
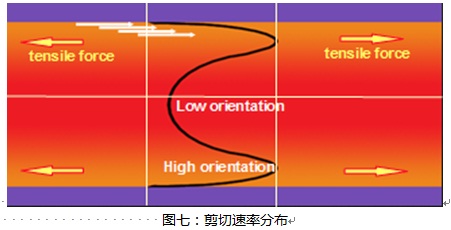
2、剪切热的作用
● 剪切变稀
剪切热的产生降低了熔体的表观粘度,提高了熔体的流动性,有利于熔体的填充,降低注塑压力及内应力,点浇口由于浇口较小,很好的利用了剪切热使熔体更容易填充,如图八所示:
● 熔体裂解
但过高的剪切速率将造成很高的剪切热使熔体发生降解,从而造成烧焦、气纹等缺陷。
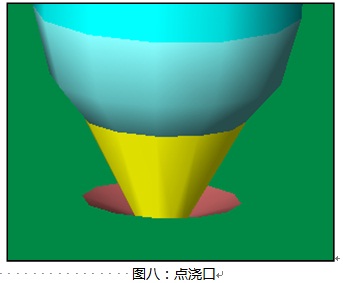
四、剪切热引起不平衡试验装置
通过实验研究在不同的注塑速率下一模多腔的流动不平衡现象,利用可视化模具、高速摄像机、集成热电偶及双料筒射出成型机可有效地观察熔体在不同工艺条件下的流动形态。
● 可视化模具:如图九。
● 高速摄像机: 观察记录成型过程中塑料熔体流动前沿在型腔内的移动情况,如图十。
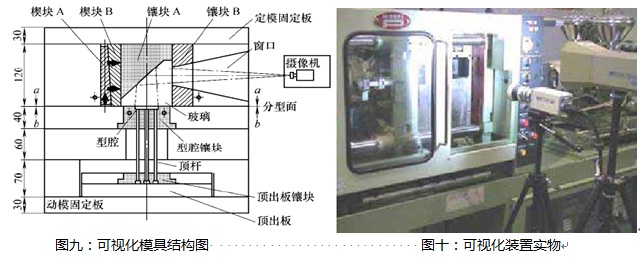
集成热电偶:如图十一。
- 可对树脂充模、冷却过程中流道剖面上的温度进行测量
- 高密度
- 高精度
- 可承受注塑熔体多次冲击
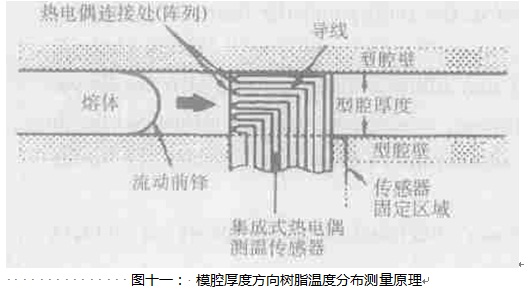
双料筒共注射成型机
● 静态可视化
● 动态可视化
采用双料筒共注射成型机进行双色切换注射的方式实现静态可视化研究,同时使用高速摄像机记录熔体注射充模流动的动态过程,如图十二所示:
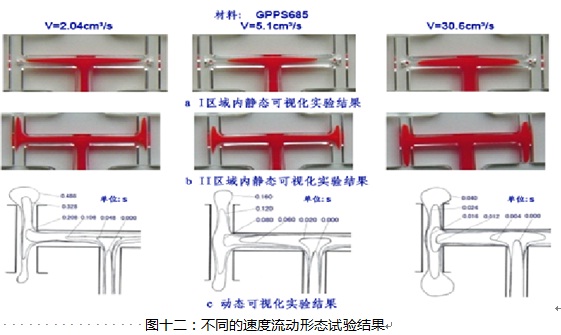
注塑材料为:GPPS685
如上图所示,分别采用低、中、高三种注塑速率下的“H”型流动形态观察发现,低速情况下熔体偏向上方分布,中速时上下熔体分布基本相同,高速情况下熔体偏向下方分布。
五、剪切热引起流动不平衡的内在机理
1、高速、低速熔体的截面温度分布
● 随着注射速率的提高熔体流动过程中会产生剪切热。式中为剪切热的表达式:
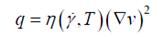
式中 :q ——剪切热
η ——树脂的粘度,它是树脂温度θ
与剪切速率γ的函数
∇v ——树脂的流动速度梯度
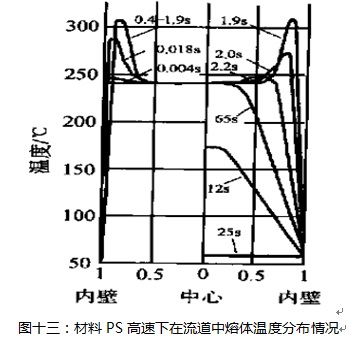
图十三所示,在高速情况下,材料PS在流道界面的分布显示中心温度较低,凝固层内侧温度最高,在普通成型工艺(中低速)温度分布是中心温度最高。
图十四所示,在不同的注塑速度下上下型腔的温度分布曲线。
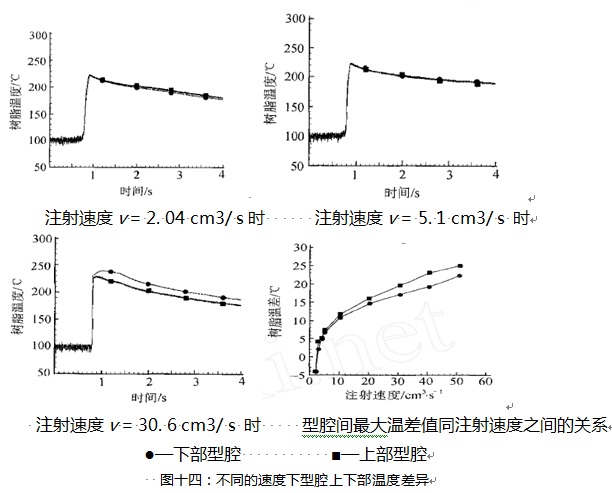
由剪切生热所导致的流道截面内熔体温度分布形态的变化以及熔体温度经过流道分岔口后的不对称现象,是造成多型腔不均衡充填的根本原因。
2、不同的流动速率对流动模型的影响
● 对“H”型流道进行高速、低速试验
● 高速注塑时下侧型腔较早填满、低速注塑时上侧型腔较早填满,图十五所示:
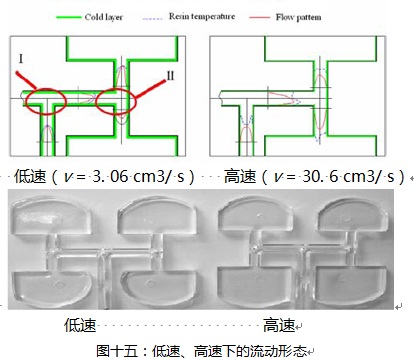
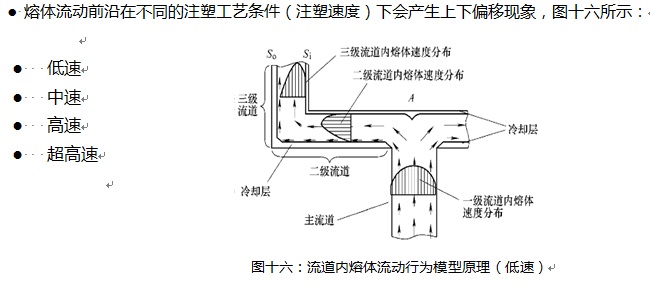
由于截面温度的分布差异使得熔体粘度差异,高温区熔体的粘度较低,流速较快,从而导致熔体流动前沿的偏移现象。
然而在超高速注塑条件下,流道内不同部位熔体的热交换也会加剧,使流道横断面方向熔体高温区与低温区之间的温度差减少,熔体进入型腔后流动前沿的偏移现象也会有所减弱。
六、moldflow分析剪切热引起的不平衡现象
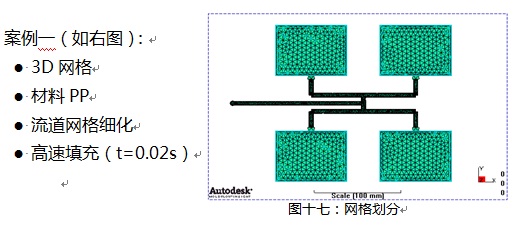
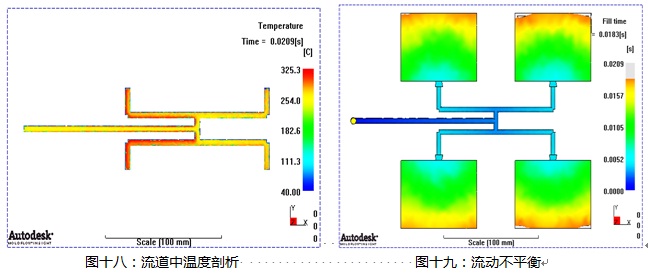
高温熔体偏离流道中心线靠近流道壁一侧分布且流动较快,最终造成不平衡充填。
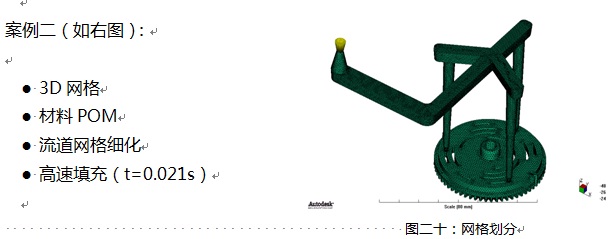
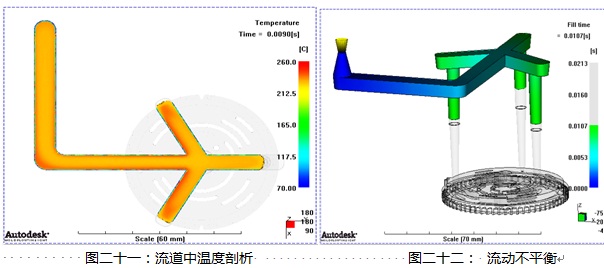
由于剪切热的作用, 主流道中不均匀但对称的熔体温度分布在二级流道中失去对称性是产生充填不平衡的根本原因。
七、改善剪切热引起不平衡现象的方法
● 更改流道、浇口尺寸,如图二十三所示:
特点:快捷方便,效果短暂,仅仅是压力平衡。
● 美国BTI研制的“MeltFlipper ”装置来改善流动平衡 将嵌件放入流道系统。这些嵌件通过旋转熔体层使之发生某种程度的取向,从而使所有较热和较冷的熔体层都被均匀分布到每一个分流道上,如图二十四、二十五所示:
特点:压力、温度、粘度均平衡
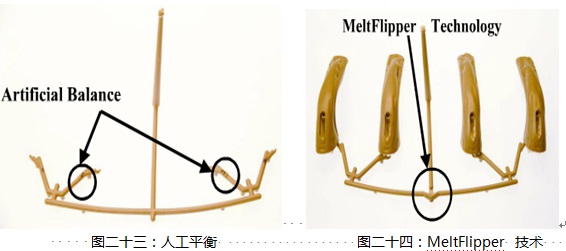
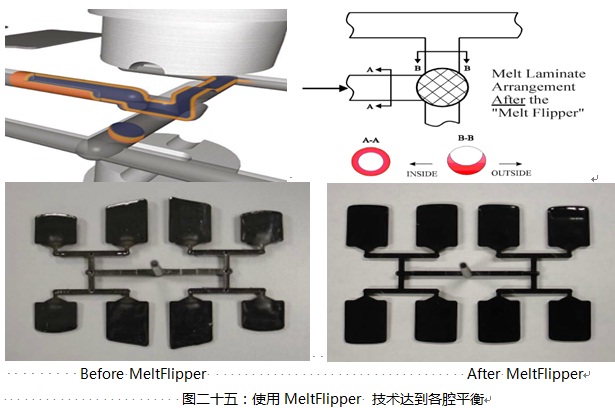
● 适当的注塑工艺,采用“两步注塑法”
两步注射法即在同一注射周期中采取从低速注射切换到高速注射的方式来改善流动平衡的影响,如图二十六:
特点:操作简易、廉价、高效。
八、结论
1、通过可视化实验证明剪切热造成各腔的熔体温度、粘度及流动模型的差异,是导致一模多腔不平衡现象的根本原因。
2、通过moldflow软件应用3D网格分析,且对流道网格细划,设定高速注塑,可以有效地模拟流道中截面温度分布不均造成的不平衡现象。
3、为了解决及预防这种由于剪切热引起的不平衡现象,可通过更改浇口,流道大小解决,但这种平衡不能本质上解决平衡问题,仅仅是压力平衡,可采用MeltFlipper装置使得进入各腔的熔体温度、粘度及压力上都达到本质的平衡,也可在工艺上尝试通过两步注塑法。